GALVANIZACIÓN
01 | 2014
Sujeciones
galvanizadas
Tuercas y pernos con recubrimientos de zinc
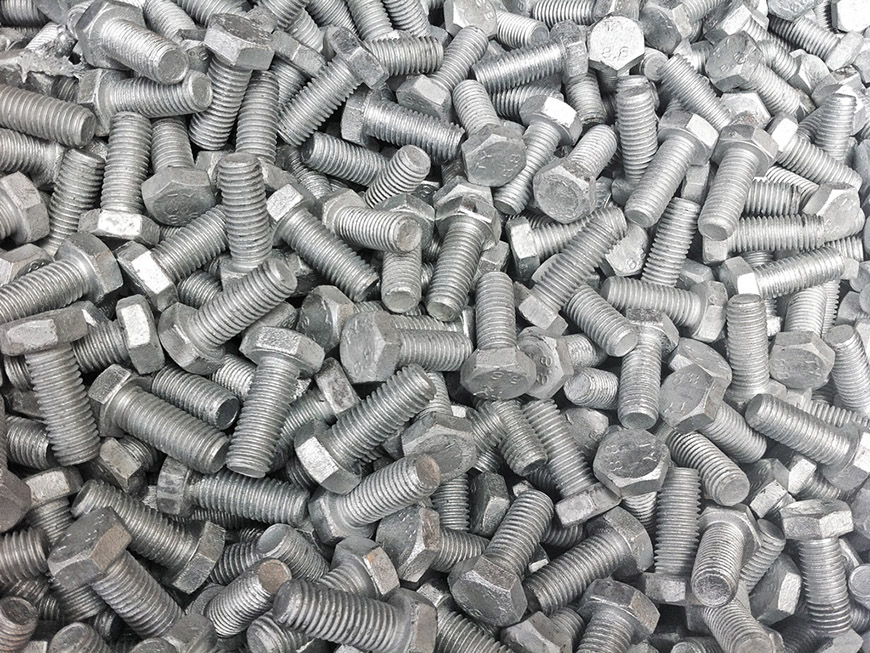
La mayoría de las sujeciones metálicas tienen un aspecto luminoso y atractivo en el momento de instalarse. Con frecuencia, tienen revestimientos delgados e incluso en un ambiente templado se oxidan tras un corto período de tiempo. De ahí que sea tan importante asegurarse de haber seleccionado el revestimiento adecuado para el entorno preciso.
Existe una amplia variedad de revestimientos metálicos que se pueden utilizar para proteger los componentes de acero pequeños, como son los elementos de sujeción. Si hablamos del uso del zinc, hay al menos tres formas diferentes de emplearlo con características muy dispares en cuanto a recubrimiento y rendimiento.
Estos tres sistemas son:
1. Galvanización en caliente por centrifugación
2. Recubrimiento Metálico con polvo de zinc (o sherardización)
3. Cincado electrolítico
Galvanización en caliente por centrifugación
El término galvanización centrífuga se utiliza para describir el proceso de galvanización en caliente de componentes roscados y otras piezas pequeñas. El proceso es muy similar a la galvanización habitual de secciones de acero grandes. Sin embargo, en este caso los componentes pequeños se colocan en contenedores perforados, permitiendo el procesado de elementos de hasta 8 mm de diámetro. Tras la inmersión en el baño de galvanización, el recipiente se centrifuga a alta velocidad de manera que el rápido giro elimine cualquier excedente de zinc para así asegurar un perfil limpio.
Cuando los artículos se sumergen en el baño de galvanización se forman una serie de capas de aleación zinc-hierro unidas metalúrgicamente a la superficie del acero. Estas aleaciones son más duras que el acero dulce y normalmente están cubiertas por una capa exterior comparativamente suave de zinc que permanece tras la operación de giro. Esta estructura es única y es lo que le da al recubrimiento galvanizado su óptima resistencia: los golpes directos son amortiguados por la capa exterior de zinc, mientras que las capas de aleación dura son las responsables de soportar la abrasión.
La norma UNE EN ISO 1461 contempla recubrimientos galvanizados que se obtienen sobre estas piezas pequeñas, con o sin partes roscadas, especificando valores mínimos para su espesor medio que están comprendidos entre 25 y 55 micrómetros (μm) según sea el espesor del material base. Las piezas de este tipo deben fabricarse con acero adecuado para galvanización y su forma debe ser también apropiada para las características del proceso. Así, por ejemplo, no son adecuadas para este procedimiento las piezas en forma de cápsulas o codos tubulares y, en general, todas aquellas que tengan orificios ciegos o zonas cóncavas en las que pueda quedar retenido el zinc.
La norma UNE-EN ISO 10684 especifica con mayor detalle las características de los recubrimientos galvanizados sobre los elementos de fijación y establece reglas para la galvanización y el mecanizado a sobremedida de las partes roscadas. La práctica más corriente es galvanizar los tornillos con sus roscas ya mecanizadas a sus dimensiones y tolerancias normales. Las roscas de las tuercas, sin embargo, se suelen mecanizar una vez galvanizadas las tuercas, con una sobremedida suficiente para compensar el aumento del diámetro de la rosca del tornillo debido al recubrimiento galvanizado. Las roscas de las tuercas se cubren con grasa o aceite neutros como protección temporal hasta su acoplamiento. Una vez montadas en sus correspondientes tornillos, las roscas de las tuercas quedan protegidas por contacto con el recubrimiento de los tornillos. Una prueba de esta protección es que las uniones con tornillos y tuercas galvanizados en caliente pueden aflojarse fácilmente después de muchos años de acoplamiento.
Revestimiento metálico con polvo de zinc (Sherardización)
Con este procedimiento se obtienen depósitos de zinc sobre pequeñas piezas mediante tratamiento de las mismas con polvo de zinc en tambores giratorios, a temperaturas inferiores a la de fusión del zinc. Los artículos han de estar químicamente limpios y secos. Cualquier agua restante puede causar problemas cuando se mezcla con polvo de zinc. Las piezas con la superficie limpia de óxidos e impurezas, junto con un 90% de polvo de zinc y 10% de polvo de óxido de zinc (para evitar la sinterización) se cargan en un tambor que se calienta a 440°C. En algunos casos se añade arena fina para ayudar a obtener una distribución uniforme. El polvo debe ser muy fino. Polvos más gruesos requieren más tiempo para formar el revestimiento deseado. La necesidad de asegurar una temperatura uniforme dentro de los barriles impone una limitación de tamaño en el proceso, que se utiliza generalmente para piezas pequeñas y bastante complejas.
Cincado electrolítico
Es un proceso de deposición electrolítica en baños (UNE EN ISO 2081 ó 10152), similar al cromado o cobreado. La capa de Zinc es mucho más fina (5-20 micras), por lo que se suele realizar posteriormente un proceso de pasivado (tratamiento que incrementa la protección). Aun así, la duración es mucho menor y en principio salvo que se recurra a pasivados caros, solo es adecuado para interiores. Como ventajas, las piezas son más suaves y uniformes aumentando su valor estético, y se pueden pasivar, lacar o pintar.
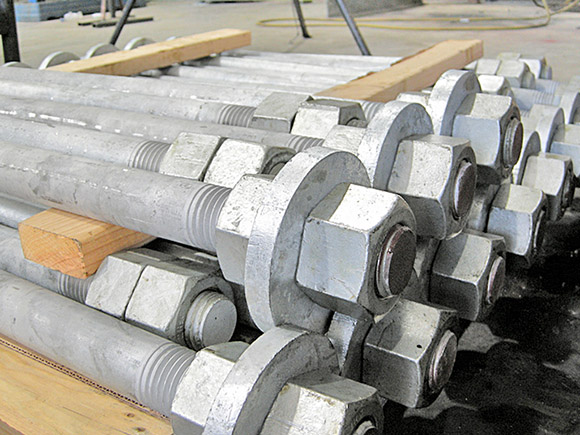